
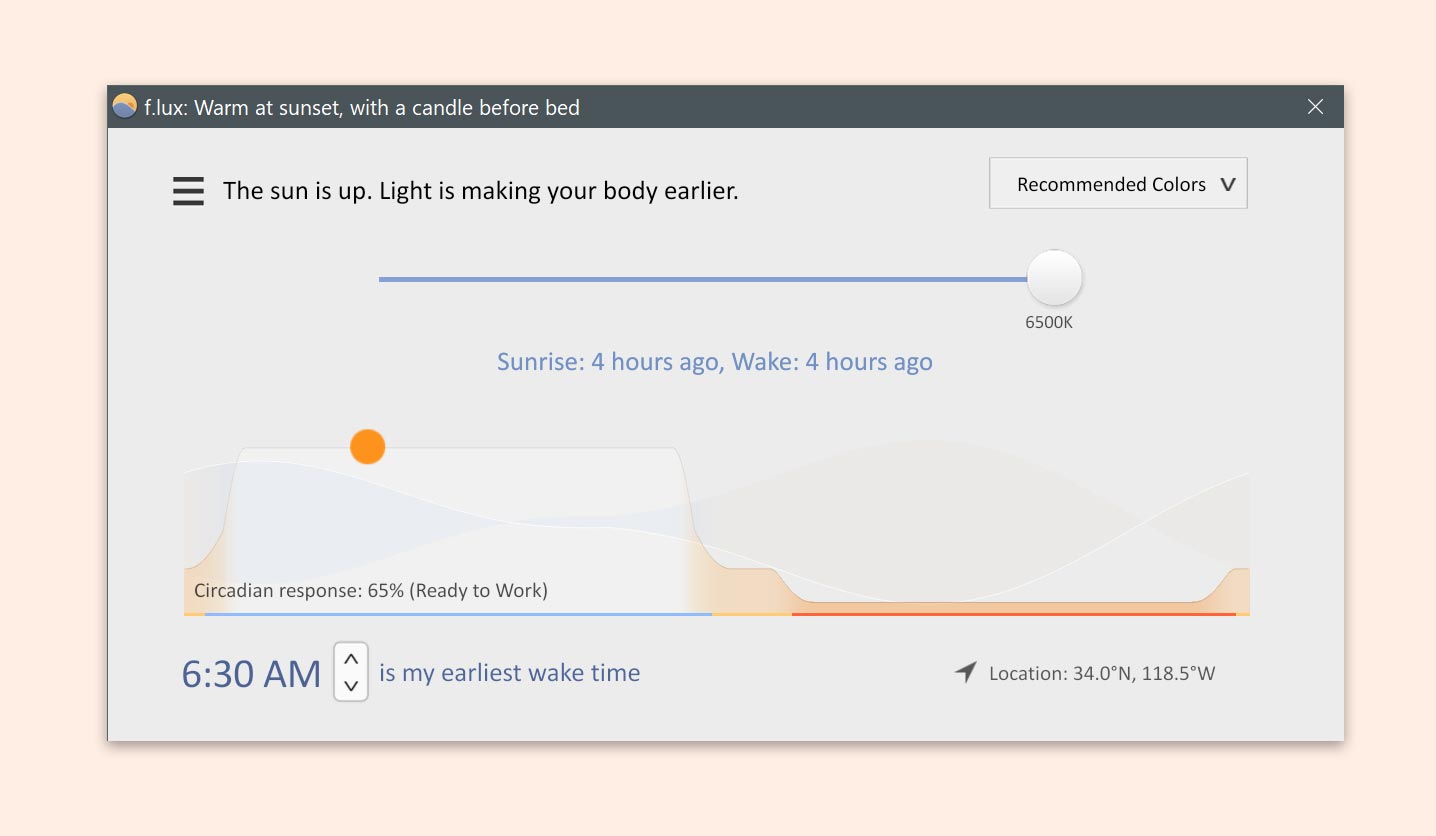
This combination represents a potential improvement over previous successful demonstrations of dish-electric technology in terms of enhanced performance, lower cost, longer life, and greater flexibility in engine design. The feasibility of competitive, modular bulk electric power from the sun may be greatly enhanced by the use of a reflux heat pipe receiver to combine a heat engine with a paraboloidal dish concentrator. Both kinds of flaws considered in this paper are of a purely deterministic nature.
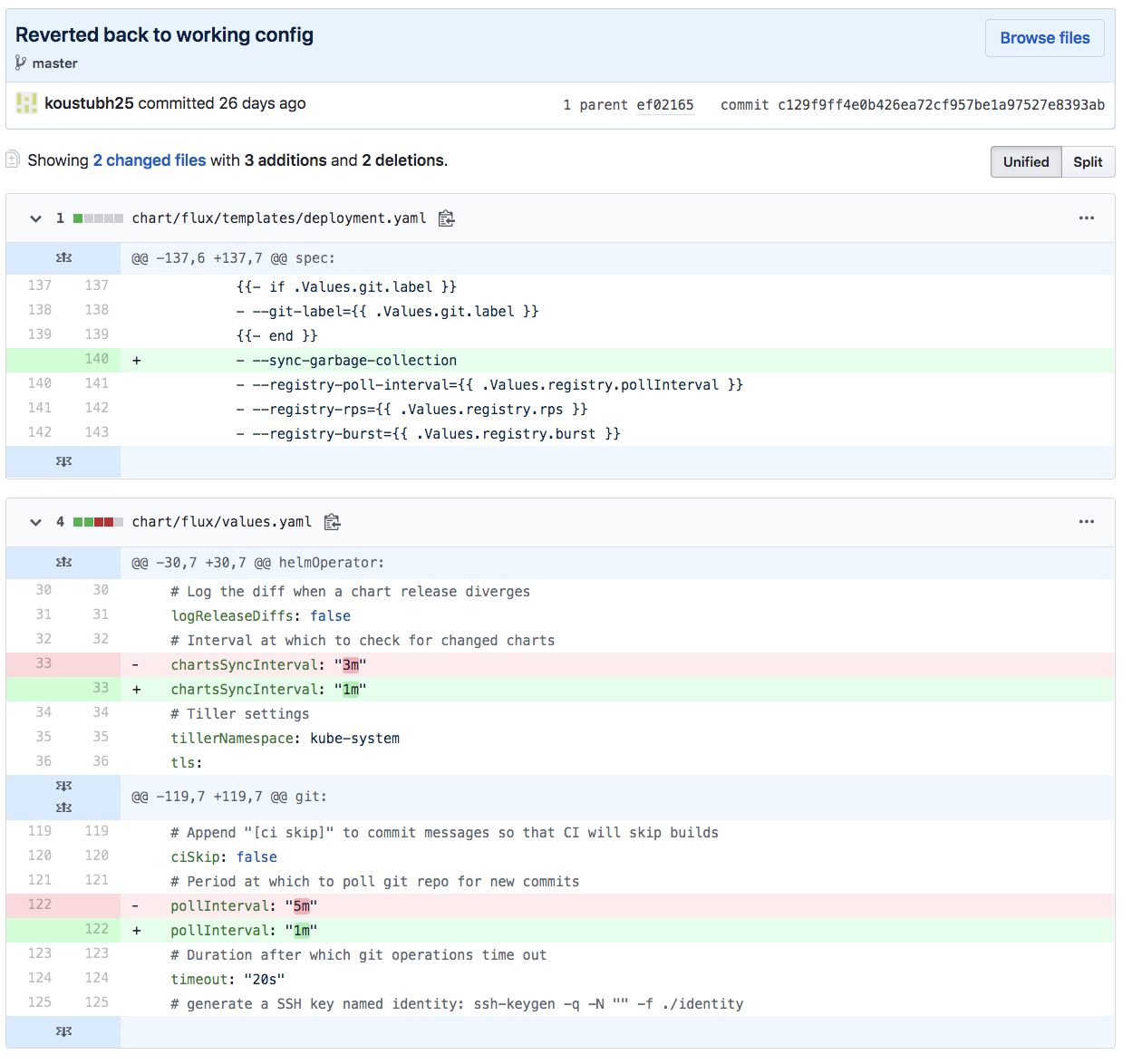
In both examples, greater than design basis loadings will occur in the receiver tubing. In the second case, sun-tracking errors give rise to axially asymmetric radiation distributions. These locally increase the radiation concentration on the receiver inside walls and tubing. The first case concerns flaws in the contour of the dish surface. Of the many possible imperfections in real collectors, two were selected which increase the loadings sustained. The purpose of this paper is to devise calculation principles which permit analysis of a receiver designed for ideal conditions to verify its structural adequacy under the nonideal conditions to be expected in reality. These two conditions cannot more » be achieved in practice, and therefore the feasible parabolic dish system is referred to as a real system although, in actual fact, it is only an approximation to any actual system. In such a system the surface of the dish is perfectly parabolic (no contour flaws are present), and the sun's central ray impinges on the dish surface parallel to the focal axis (no sun tracking flaws are present). For an axially symmetric cavity receiver with a parabolic dish collector, it is simple to determine the insolation pattern on the receiver internal surfaces if the system is ideal. The absorption of solar heat and the attendant thermal and mechanical loadings on the tubes of cavity receivers depend predominantly on the flux distribution of the incident solar radiation. It also has the advantage that it can accommodate a number of internal surface orientations and has been shown to agree very well with more sophisticated computer programs. CAV was selected as a starting point for this development because of its availability and because more » it interfaces with a thermal analysis program called CVT. The principal interest was in obtaining the overall flux distributions within arbitrarily shaped cavities. The objective of this effort was to develop a design tool with which the effects of concentrator and receiver geometry on energy distributions could be investigated. Solar receivers are heat exchangers and incident flux distributions are a fundamental aspect of their design. Knowing the incident flux distributions provides the designer with insights such as where hot-spots are likely to occur, where heat exchange surfaces are needed, and where more detailed analysis might be warranted. This information is needed ultimately to determine the resulting energy fluxes to the working fluid, temperature distributions within the cavity, and receiver performance. For detailed design of cavity receivers, however, it is necessary to determine the incident flux distribution on the interior surfaces. Together with simplifying assumptions about cavity absorptance, emittance, and convective losses, good estimates of the dish-receiver collection efficiency as a function of incident flux and effective cavity temperature can be obtained.
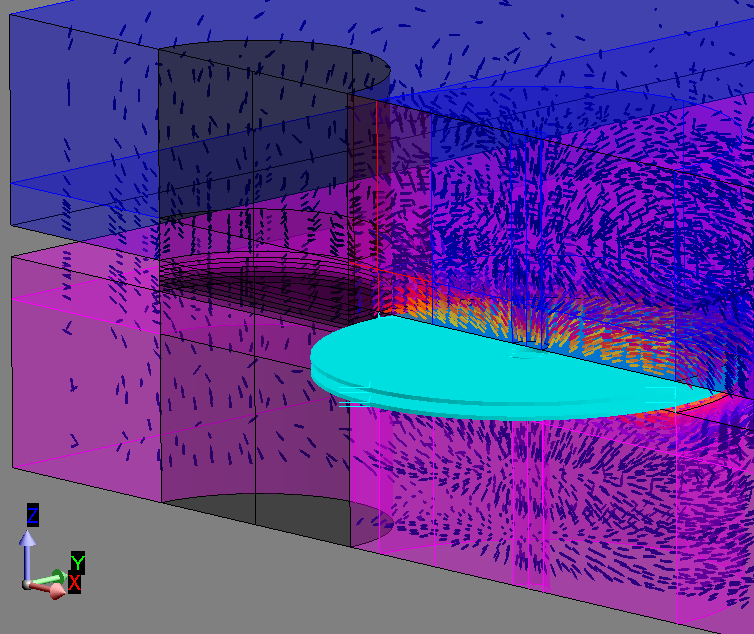
Apply correction for air density fluctuation using Webb et al., 1980.Correct sonic temperature for the effect of humidity following van Dijk et al., 2004.Apply high frequency corrections following Moncrieff et al., 1997 Massman, 2000, 20001 or Horst, 1997.Apply low frequency correction following Moncrieff et al., 2004.Lag CO 2 and H 2O measurement against sonic wind measurement for maximization of CO 2 and H 2O flux (Horst and Lenschow, 2009 Foken et al., 2012).Apply coordinate rotation with an option to use the double rotation method (Tanner and Thurtell, 1969) or planar fit method (Wilczak et al., 2001).Despike and filter data using sonic anemometer and gas analyzer diagnostic codes, signal strengths, and measurements output range threshold.Also provides many other variables of atmospheric properties, instrument diagnostics, and intermediate corrections. Provides fully corrected outputs of CO 2 flux, latent heat flux, and sensible heat flux at a user-defined interval (e.g., 30 minutes).
